Protective Coating Application
Coating Application
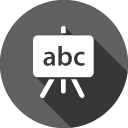
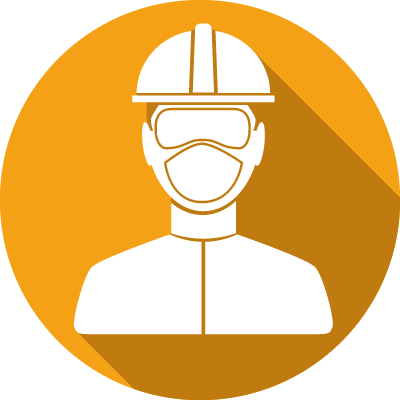
Lesson Complete:
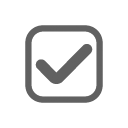
Lesson Viewed:
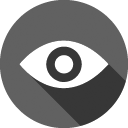
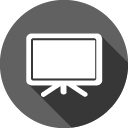
Lesson 1 - Relative Humidity and Dew Point
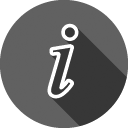
Objective
To understand and how to measure relative humidity and dew point, and their effect on coating application and cure.
- Relative humidity and dew point have an effect on surface preparation and coating application.
- Relative humidity and dew point have an effect on coating, overcoating, cure and long-term performance.
- Protective coatings personnel should know the implications of relative humidity and dew point.
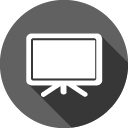
Lesson 2 - Steel Temperature
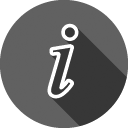
Objective
To understand how to measure and assess steel temperatures and the effect on paint application
- Steel temperature is related to the overall environmental conditions.
- Steel temperature is generally specified within the paint specification.
- Too high or low steel temperature can affect coating application, drying, cure and performance.
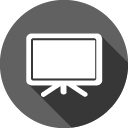
Lesson 3 - Brush Application
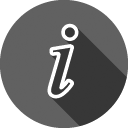
Objective
To understand how, where and when a brush can be used in the industrial coating industry. To understand the advantages and disadvantages of brush application
- The protective coatings applicator will almost certainly use a brush during coating operations.
- The most simple of application tools.
- Various types and sizes available.
- Used with most coatings for full coatings, stripe coatings etc.
- Limited application thickness.
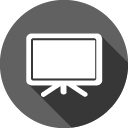
Lesson 4 - Roller Application (inc.mitt, trowel etc)
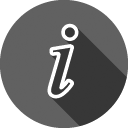
Objective
To understand how, where and when a roller can be used for the application of heavy-duty coatings. To understand the advantages and disadvantages of roller application.
- The protective coatings applicator will use a roller in their duties.
- A common form of coating application for large areas.
- Rollers can be used with various coatings.
- The process is simple to use.
- The equipment is relatively inexpensive.
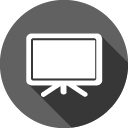
Lesson 5 - Airless Spray (Introduction)
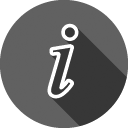
Objective
To give the protective coating applicator an appreciation of airless spray painting and its use for the application of industrial coatings.
- One of the most common forms of coating application.
- Must be conducted by trained operatives.
- Ideal for factory and site application.
- Capable of large volume application.
Prior to conducting any spray painting the protective coatings applicator must successfully complete the spray painting training units.
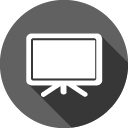
Lesson 6 - Air Assisted Spray (Introduction)
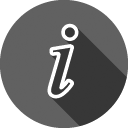
Objective
The objective of this training segment is to give the protective coating applicator an appreciation of air-assisted including conventional and HVLP spray painting and its use within the industrial coatings.
- Air-assisted spray painting is a common method of coating application, especially factory applied coatings.
- Air is required to assist coating application.
- Air-assisted spray painting is restricted to selective coatings.
- Air-assisted spray painting generally applies thinner coats as opposed to an airless spray.
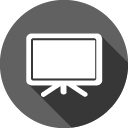
Lesson 7 - Wet Film Thickness
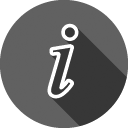
Objective
To measure the wet film thickness of an applied coating. With a knowledge of the target dry film thickness and the volume solids of the paint, the applicator can calculate the required wet film thickness at which the paint must be applied.
- The protective coatings applicator should be able to calculate the wet film thickness of most applied coatings.
- Most coatings have a different wet film thickness from the dry film thickness.
- The film thickness at the applied stage cannot be calculated without knowing the required wet, and ultimately, the dry film thickness.
- The calculation and process is a simple method.
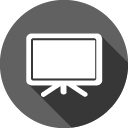
Lesson 8 - Dry Film Thickness
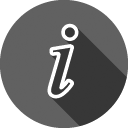
Objective
To measure the dry film thickness of applied coatings by non-destructive testing methods.
- Only method of dry film thickness that can be obtained without destroying the dried film.
- There is a direct correlation between the wet film thickness and dry film thickness.
- Tests are usually conducted by Supervisors, QC or Managers.
- Dry film thickness assessment is a simple test method but procedures do differ.
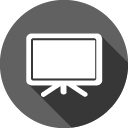
Lesson 9 - Drying and Recoating (inc, cure)
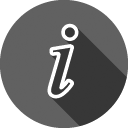
Objective
To understand the drying and recoating process of industrial coatings.
- All coatings have some sort of a drying process.
- The drying and recoating times are different.
- The drying and recoating times will be defined on the product data sheets.
- The drying and recoating periods are affected by temperature and environmental conditions.
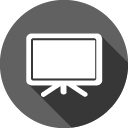
Lesson 10 - Stripe Coating
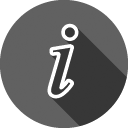
Objective
To understand why and when stripe coats should be applied in a protective coating system.
- The protective coatings applicator will conduct stripe coating in their application role.
- Stripe coating is always recommended for steel protection.
- Stripe coating is generally applied by brush.
- Stripe coating provides additional protection to vulnerable locations.
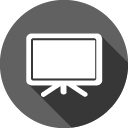
Lesson 11 - Surface Cleaning
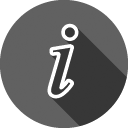
Objective
To understand the cleaning requirements prior to paint application.
- Paint coatings require clean surfaces to ensure the correct level of adhesion is achieved.
- There are numerous types of surface contaminants which could have an adverse effect on coating adhesion.
- The protective coatings applicator will be required to recognise and remove surface contaminants prior to coating application
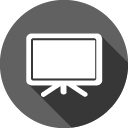
Lesson 12 - Coating Damage and Repair
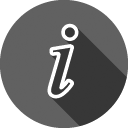
Objective
To understand remedial paint application procedures for damaged coated surfaces. Coatings may be damaged:
- During handling and transportation.
- During site erection.
- By other trades.
- By general wear and tear in service.
The protective coatings applicator will almost certainly repair damaged coatings/conduct coating maintenance.
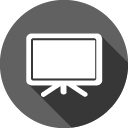
Lesson 13 - Materials and Equipment Handling
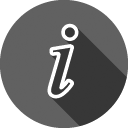
Objective
To understand the basic handling procedure during paint operations.
- The protective coatings applicator will handle various materials during their duties.
- Materials could be heavy, awkward, flammable or toxic.
- Plant and general application equipment may have to be delivered, moved and stored on a daily basis.
- You will not necessarily find handling instructions with equipment.
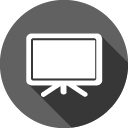
Lesson 14 - Shop Painting
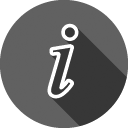
Objective
To give the protective coatings applicator an understanding of the shop painting process and the duties that may be expected from the protective coatings applicator.
- Majority of items are prepared and coated in factory facilities.
- The size, type and location of paint shops varies considerably.
- Paint shops can be independent or part of a fabrication facility.
- Temporary paint shops are available for specific contracts.
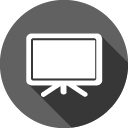
Lesson 15 - Site Painting
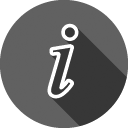
Objective
To understand the implications of conducting site painting activities.
- The protective coatings applicator will generally conduct some site painting in their duties.
- Site painting has more Health, Safety and Environmental issues than shop painting.
- Most industrial work-painting is conducted on site.
- Every site can be completely different to the next site.
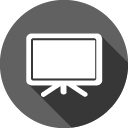
Lesson 16 - General Maintenance - Plant and Equipment
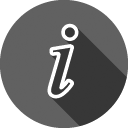
Objective
To understand the requirement for general maintenance of plant and equipment in the coatings industry.
- The protective coatings applicator will use a number of items of plant and equipment during their duties.
- Major maintenance is usually conducted by trained fitters or electricians.
- Plant and equipment are used for preparation, coating application and associated activities such as cleaning, grit removal etc.
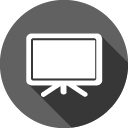
Lesson 17 - Equipment Cleaning
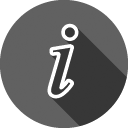
Objective
To understand the requirement for cleaning plant and equipment following coating application.
- The protective coating applicator will conduct equipment cleaning as part of their duties during paint application.
- Cleaning equipment correctly will extend the life of the equipment.
- Cleaning equipment will ensure minimal contamination on the future use of the equipment.
- General equipment consists of brush, roller and some spray equipment.
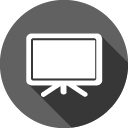
Lesson 18 - Maintenance Painting Operations
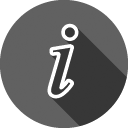
Objective
This training unit will review the elements of maintenance painting.
The unit specifically relates to external onshore steel structures.